Okay, so the other day, the old generator started acting up again. Sputtering, dying, the usual signs pointing towards fuel issues. Figured it was time to dive into the carburetor, specifically suspecting that little float inside.
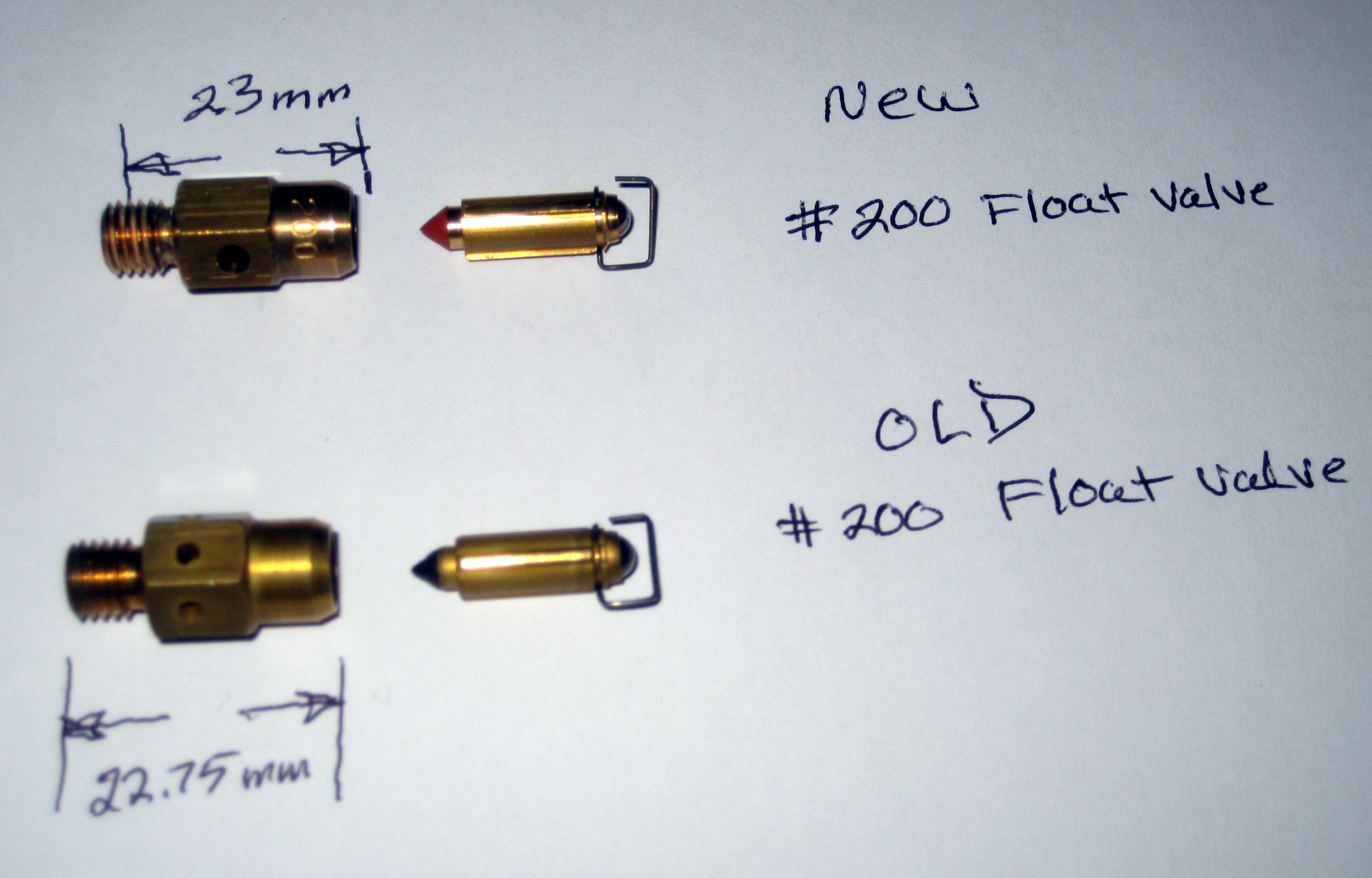
Getting Started
First thing, gotta get the carb off. Shut off the fuel line, disconnected the linkage cables – always a bit fiddly, those tiny clips. Loosened the bolts holding it to the engine block. Took a bit of wiggling, but it came off clean. Laid out some old rags on the workbench ’cause carbs always drip a little fuel, no matter how careful you are.
Inside the Bowl
Next up, the float bowl. Usually held on by a few screws or sometimes a central bolt. Mine had four small screws. Easy enough. Popped the bowl off, careful not to spill too much of the remaining gas. And there it was, the float assembly, sitting right there.
The float itself, usually plastic or brass, just sits there attached to a little hinge pin. Its job is simple: float up when the fuel level is right, pushing a tiny needle valve shut to stop more fuel coming in. If it gets stuck down, too much fuel floods in. If it gets stuck up, or leaks and sinks, not enough fuel gets through, or it just plain overflows.
Checking the Float
My first check was simple: does it move freely? Gave it a gentle push up and down on its hinge. Seemed okay, no obvious sticking. Pulled the little hinge pin out – sometimes they just slide out, sometimes there’s a clip. Mine slid right out. Lifted the float and the attached needle valve away.
Then I looked closely at the float itself. It was a plastic one. Held it up, shook it gently. Was listening for any sloshing sound, which would mean fuel had leaked inside, making it heavy and not float right. Nothing. Good sign. Checked for any cracks or pinholes. Looked solid.
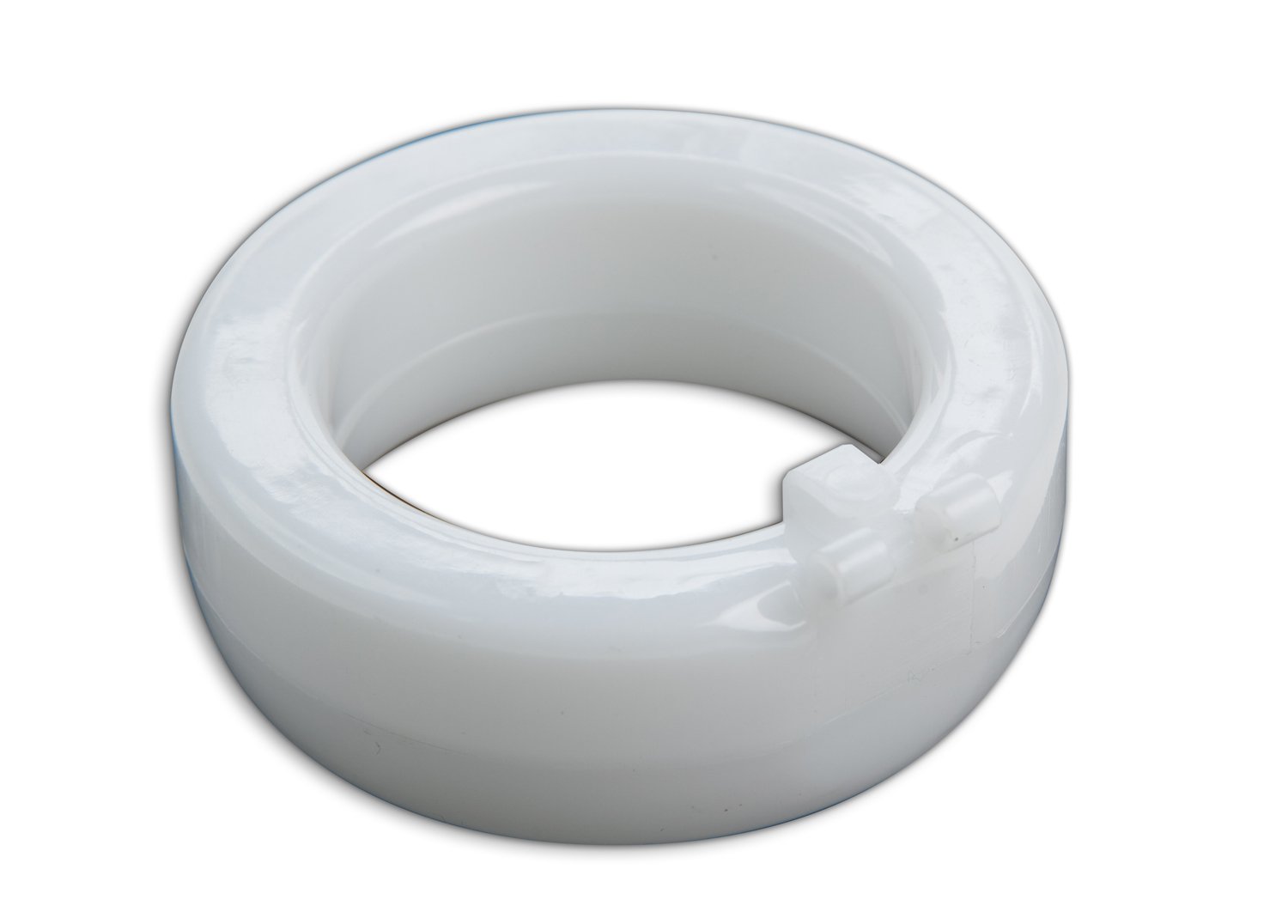
Next, the needle valve. Checked the little rubbery tip. Sometimes they get worn or grooved, letting fuel seep past even when closed. This one looked surprisingly decent. Also checked the seat where the needle sits – made sure it was clean, no debris.
So, if the float wasn’t leaking and the needle looked okay, what was the issue? Sometimes, the float level gets out of whack. There’s usually a tiny metal tab on the float arm that pushes against the needle valve. Bending this tab slightly changes the level at which the fuel shuts off.
The Adjustment
I didn’t have the exact spec for the float height handy, but based on experience, it looked maybe a little low (meaning the fuel level would be too high before shutoff). Took some needle-nose pliers and gave that tiny tab a very slight bend upwards. We’re talking fractions of a millimeter here. It doesn’t take much.
- Checked free movement again.
- Made sure the needle valve still seated properly.
- Cleaned out the float bowl itself – found a tiny bit of sediment in the bottom, which definitely doesn’t help things. Sprayed it out with carb cleaner.
Putting it Back Together
Reassembly is just the reverse. Put the float and needle back, slide the hinge pin in. Carefully put the float bowl back on, making sure the gasket was seated right. Tightened the screws. Bolted the carb back onto the engine, reconnected the fuel line and linkages.
Turned the fuel back on. Waited a moment. Crucially, no leaks. That’s always the first hurdle passed.
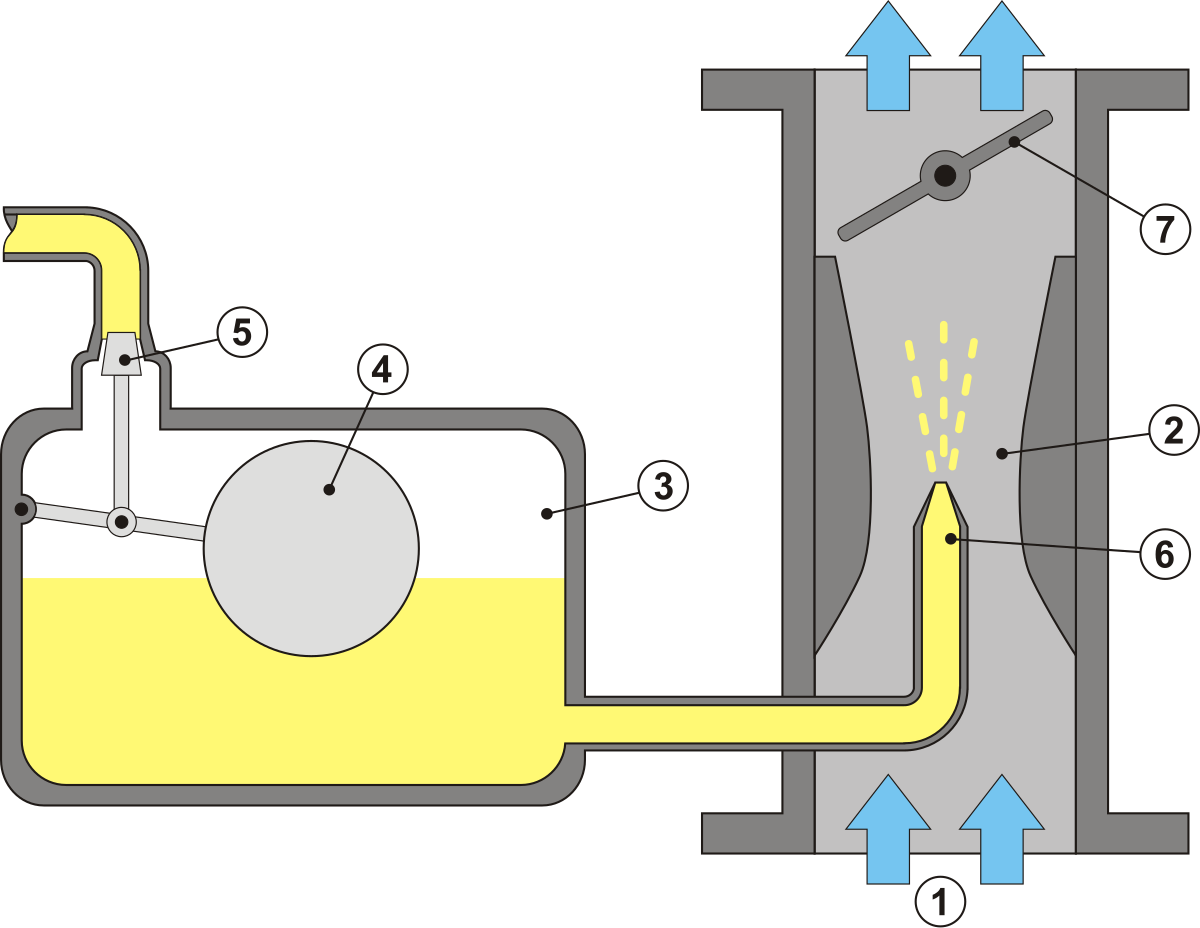
Pulled the starter cord. Fired up on the second pull. And wouldn’t you know it, purring like a kitten. Or, well, as much as this old generator can purr. Let it run for a good 10 minutes, stable and smooth. Seems like that little float adjustment and cleaning did the trick.
It’s often the simple things inside these carbs. Dealing with floats isn’t black magic, just takes a bit of patience and careful observation.