Alright folks, so I’ve been digging into this ironface coating thing lately. Honestly, I kept hearing whispers about it online, especially folks raving about how tough it makes metal stuff. Sounded kinda sci-fi, right? “Ironface”? Like putting an actual face on iron? Figured I better get my hands dirty and see what the fuss is really about. Wanted to understand what it is, what it does well, and where you’d actually use it today.
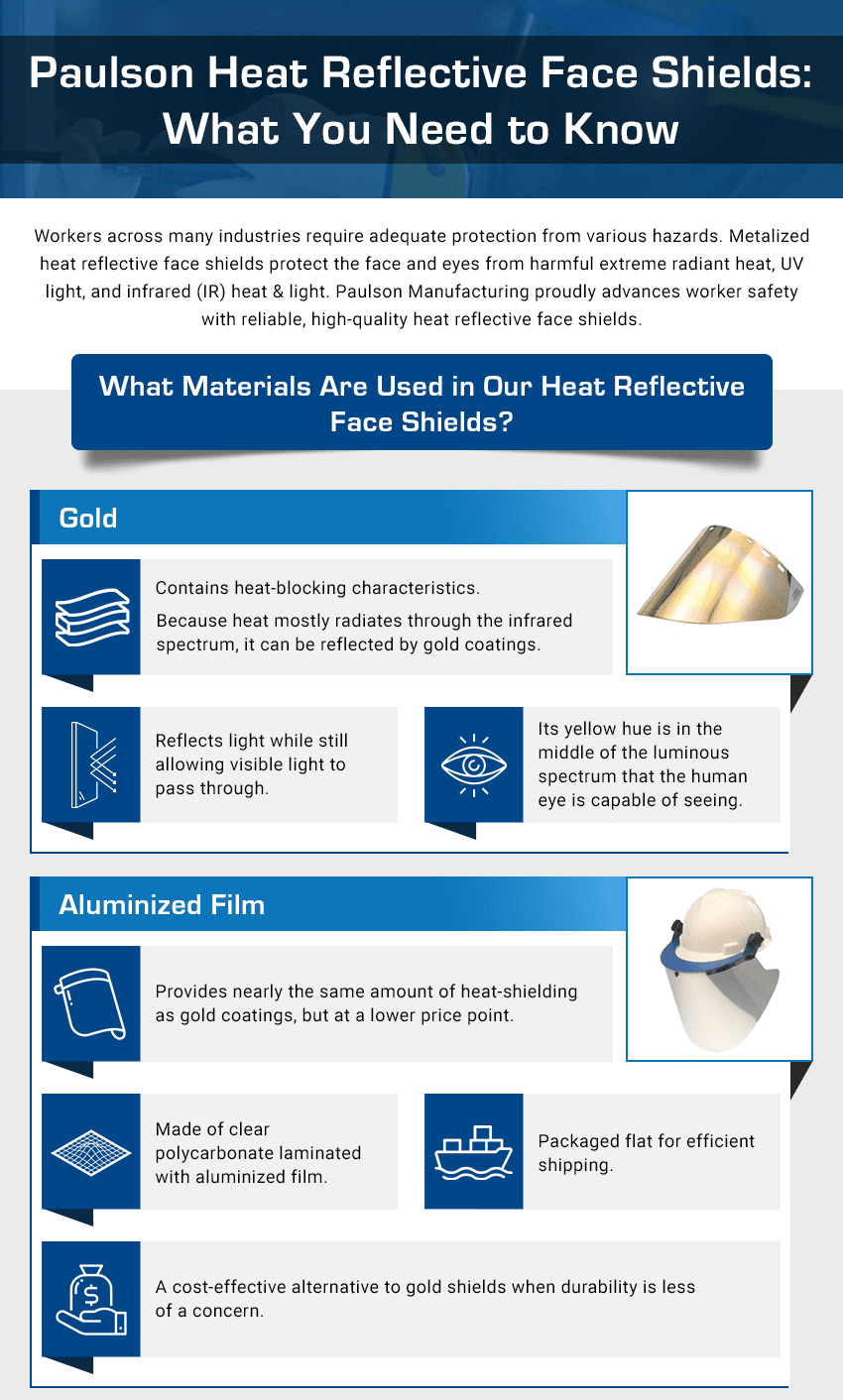
Starting Out: What Even Is This Stuff?
My first stop was pure confusion. Saw the name “Ironface coating” everywhere, but nobody just came out and explained it plain. It felt like trying to crack some secret code. Everyone assumed you already knew the basics! So, I grabbed my metaphorical shovel and started digging deeper. Watched some videos, skimmed forum threads, read product descriptions until my eyes crossed. Here’s the simple truth I pieced together:
- It’s NOT a layer of actual iron. That was my biggest surprise! The “iron” part seems more about giving iron-like properties.
- It’s basically a super hard, tough resin-based paint. Think of it like super glue mixed with paint particles and baked hard.
- You put it on stuff. Mainly metal things – tools, machine parts, that kind of gear. Maybe some plastics? Needs a super clean surface though!
Okay, basic box checked. Now, what’s the big deal? Why bother?
Testing the Hype: My Garage Experiments
Talk is cheap. I needed to see it work. Found a small, relatively affordable starter kit online (took some searching!). Scrounged up some sacrificial victims from my workshop:
- An old, slightly rusty wrench.
- A clean but shiny new bracket.
- A chunk of metal pipe scrap.
Step one: Preparation is EVERYTHING. Seriously, if you skip this, you might as well not bother. I learned the hard way on my first attempt (the wrench). Rinsed it? Yep. Thought that was enough. Nope! Tried applying the coating right after a quick wipe. Big mistake. It beaded up, slid off, looked awful. Felt like painting on a greasy plate. Total waste. Had to completely strip it back with strong cleaner and sandpaper. Felt like I’d already done a day’s work before even opening the coating!
Second try (with the bracket): Went full surface prep ninja.
- Degreaser bath? Check.
- Painstaking sanding? Check (ugh, my arms!).
- Rinse and dry? Double check.
Applying the coating itself was… interesting. The stuff has a weird smell. Not terrible, but definitely “chemical-y”. It’s kinda runny at first, so you gotta be careful with drips. Followed the instructions religiously – thin coats, time to dry, then the magic step: baking. Popped the bracket into my old toaster oven in the garage. Waited, smelled more chemical smells. Pulled it out… and wow. The shine was different. Like a deep, hard candy shell. Felt amazingly smooth and slick to the touch. Okay, this felt more promising!
Putting It To The (Punishing) Test
Now came the fun part. What did this shiny coat actually do?
1. Scratch Test: Took another wrench (didn’t coat this one) and firmly dragged the edge across my coated bracket. Held my breath… On bare metal? Deep, ugly gouge. On the coated section? Just a faint silvery line that wiped off mostly with my finger! Serious scratch protection.
2. Rust Test: Took my coated pipe scrap and the coated wrench (finally did it right!). Also left out an uncoated piece of similar metal. Spritzed them all lightly with salty water every day for a week, keeping them damp and miserable. The uncoated piece looked like an artifact pulled from a shipwreck after just a couple of days. The coated ones? Zero rust. Nada. Not even a stain. Just wiped the salt crust off, good as new. Corrosion resistance? Totally legit.
3. Friction/Glide: Tried rubbing the coated bracket against another piece of metal. Almost slipped out of my fingers it was so slick! Definitely reduces friction – makes stuff slide easier.
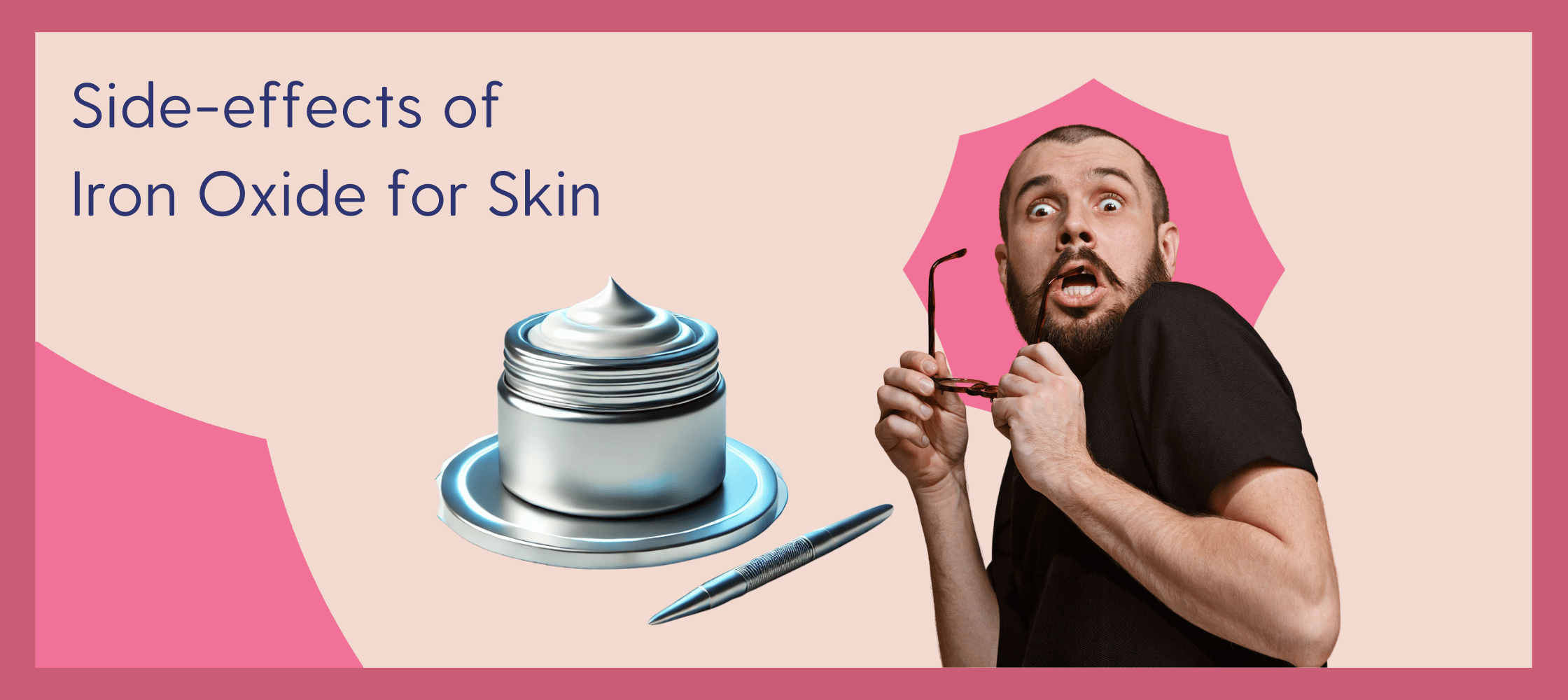
So, Who Should Actually Use This Stuff Today?
Here’s what my messing around convinced me of. It’s perfectly suited for specific, tough jobs where you need:
- Serious scratch resistance on tools that rub or impact things.
- Super corrosion protection, especially in damp or salty conditions.
- To make things slippery for moving parts or to stop stuff from sticking.
Think:
- High-use tools: Wrenches, sockets, pliers – anything clanging in the toolbox.
- Outdoor equipment parts: Hinges, latches, brackets on trailers, boats, machinery facing the elements.
- Machinery components: Slides, bushings, shafts where you want less friction and more protection.
- Restoring/Protecting collectibles: Old tools, car parts you want preserved.
Would I coat my kitchen sink? Nah. Regular paint on a bookshelf? Overkill. But for the tough stuff that needs serious armor? This Ironface coating delivers. It’s fussy to apply right, gotta respect the prep, but the payoff on the right project is massive. Less replacing rusty tools, less sticking parts, less frustration. Just gotta pick your battles!